Introduction
As part of the European Green Deal and the new Circular Economy Action Plan, the European Commission has undertaken a revision of Directive 94/62/EC on packaging and packaging waste. This directive, adopted by the Council of the European Union on December 20, 1994, was originally developed to prevent or reduce the environmental impact of packaging and packaging waste. In addition to limiting heavy metals such as lead, cadmium, mercury, and hexavalent chromium to minimal levels, the directive set out the “essential requirements” — the foundation for the design and use of packaging, based on the core principles of Reduction, Reuse, and Recycling, now commonly referred to as the “3Rs.”
The new regulation, REGULATION (EU) 2025/40 — also known by its acronym PPWR (Packaging and Packaging Waste Regulation) — aims primarily to ensure a market in which all packaging is either reusable or recyclable in an economically viable way by 2030–2035. It reinforces the essential requirements and establishes concrete implementation targets.
Unlike the previous directive, this is now a regulation, which means it is directly applicable in all Member States upon entry into force, with no need for national transposition.
The PPWR was formally adopted by the European Parliament and Council on December 19, 2024, and entered into force on February 11, 2025 — 20 days after its publication in the Official Journal of the European Union on January 22, 2025. It will become applicable as of August 12, 2026 — 18 months after its entry into force.
With over 70 articles and additional delegated acts still pending publication, a few pages would not suffice to cover the full scope and complexity of the Packaging and Packaging Waste Regulation (PPWR). This publication is not to be considered legally binding or as a guarantee of compliance with the Regulation (for legal purposes, please refer to the full text of the Regulation). Link to the full text
This regulation is expected to help the European Union move closer to becoming a “recycling society,” where the impact of packaging becomes a shared responsibility, aimed at preventing waste generation and using waste as a resource. Naturally, this transition cannot happen without a robust system for take-back, collection, recovery of packaging waste at the end of its life cycle, and transformation into a resource for new production. Member States are therefore actively involved in this process.
What is packaging, and why is it used?
“Packaging”: an article, regardless of the material it is made from, intended to be used by an economic operator to contain and protect products or to enable their handling, transport, or display to another economic operator or to the final user. Packaging may vary in format depending on its function, material, and design.
Packaging also serves as a communication tool for consumers: it informs them about the product it contains, how to use it, whether it is hazardous, and now more than ever, what to do with the packaging once it is empty—can it be reused, does it become waste, and if so, what material is it made of and where should it be disposed of?
To ensure better coordination of collection systems, the regulation also provides for the marking and identification of the material(s) used in the packaging. The goal is to harmonize labeling across the European Union, making it easier to correctly separate packaging waste at the source.
As a result, every package, whether empty or containing a product placed on the Union market, will be required to bear harmonized labeling. While the exact specifications are not yet finalized, the European Commission is expected to adopt implementing acts by August 12, 2026 to establish these harmonized labeling rules.
Packaging may be mono-material (or single-layer), meaning it is made from one type of material throughout. This greatly facilitates sorting and recycling: with simpler separation or breakdown processes, mono-material packaging enables more efficient and effective recycling.
In some cases, to enhance product protection, packaging is made of multiple materials, each offering specific properties. These are referred to as multi-material packaging.
Such packaging may also be multi-layered, with layers glued together. The layers may all be of the same material category (e.g., plastic, cardboard, metal) or of different categories. This is common for food-contact packaging, where one or more layers of plastic may be combined with a metal layer to create a barrier—preventing migration of substances between layers. However, separating these layers can be extremely difficult, or even impossible.
There are also packaging solutions made up of separate components of different materials, which can be disassembled manually or mechanically. An example is aluminum bottles with plastic sleeves, where each part is mono-material and suitable for its own specific recycling stream. Tournaire offers such solutions under the SYSTEM PLUS™, AP25™, AP28™, and CHEM 42™ ranges for machine separation, and OMNI PLUS™ for easier manual disassembly.
So, what exactly does the PPWR regulate?
The PPWR introduces major changes for companies manufacturing or placing primary, secondary, or tertiary packaging on the EU market. It regulates packaging materials, associated waste, and design requirements. The regulation specifically applies to economic operators and producers.
The PPWR is structured into 13 chapters, covering the following key measures:
- Recyclability
- Post-consumer recycled content (PCR)
- Waste reduction
- Reusability
- Labeling
- Registration and reporting
In addition, the PPWR requires that sanctions be “effective, proportionate, and dissuasive,” though the interpretation of these terms may vary between EU Member States. Its implementation may therefore carry significant compliance risks for businesses.
Among the provisions, Article 6 defines recyclable packaging, stating that packaging is considered recyclable if it is designed to enable the recycling of materials in such a way that the resulting secondary raw materials are of sufficient quality to replace the original primary raw materials.
By January 1, 2030, all packaging placed on the market must be recyclable.
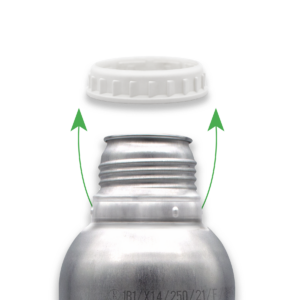
By January 1, 2035, once the packaging becomes waste, it must be able to be separately collected and directed to specific waste streams, without compromising the recyclability of other streams, and be recyclable at scale.
From an industrial standpoint, 2030 is right around the corner — businesses must act now to anticipate and adapt to these changes.
All packaging must be designed and intended to be recyclable at end of life. This means it must be:
- Easy to separate at source;
- Sorted into specific waste streams without contamination;
- Recycled at industrial scale.
The PPWR seeks to standardize recyclability criteria across the EU to remove internal market barriers. Packaging will therefore be classified as A, B, or C, based on how well its design meets the recyclability criteria set out in Tables 3 and 4 of Annex II.
Additional milestones are established to support the EU’s ambition toward a circular economy:
- From 2030: Packaging must meet the defined recyclability criteria to be considered recyclable.
- From 2035: Additional requirements based on actual large-scale recycling outcomes will apply. Packaging rated below C will be deemed technically non-recyclable, and its placement on the market will be restricted.
- From January 2038: Only packaging rated B or above will be allowed on the EU market.
This provision also lays the groundwork for adjusting the financial contributions producers must make under the Extended Producer Responsibility (EPR) scheme — linking the economic responsibility of producers to the recyclability quality of their packaging design.
When it comes to recycling, metal offers several advantages. It can be melted down and reused infinitely without any loss in material quality. Furthermore, using recycled metal to produce new products can save up to 95% of the energy required for primary production from virgin materials — a particularly notable benefit in the case of aluminum.
Minimum recycled content in plastic packaging
According to Article 7, any plastic component of packaging placed on the market must contain the following minimum percentage of recycled content derived from the recovery of post-consumer plastic waste, calculated as an annual average per manufacturing plant.
Packaging must be designed and manufactured in such a way as to promote the increased substitution of virgin raw materials with recycled materials. The recycled content must come from post-consumer plastic waste collected within the EU or in a third country, provided that the collection standards are equivalent.
These targets aim to encourage innovation in recycling technologies and to ensure uniform standards across the EU market—a goal already pursued in France with the AGEC Law (Law No. 2020-105 of 10 February 2020 on combating waste and promoting the circular economy).
Minimization of packaging
Article 10 states that packaging placed on the market must be designed so that its weight and volume are minimized to the extent necessary to ensure its functionality, taking into account its shape and the material it is made of.
The inclusion of features that artificially increase perceived volume, such as double walls or false bottoms, or the use of non-essential extra packaging, is prohibited. However, any additional weight or volume that improves recyclability or reusability is justified and accepted.
Manufacturers will be required to provide documentation that demonstrates compliance with PPWR regulations. This will include data on minimum required weight and volume, along with the calculation method used.
Exceptions may only apply to products registered or protected before February 11, 2025, if the new requirements would compromise the distinctive character or integrity of these protected designs or models.
Excessive packaging depletes resources and creates unnecessary waste. By optimizing packaging, companies not only comply with regulatory standards, but also reduce costs, enhance their sustainability credentials, and strengthen their environmental reputation. For consumers, less packaging means less waste, promoting more sustainable consumption habits.
Reusable packaging
Article 11 sets out the criteria that packaging must meet in order to be considered reusable, such as the ability to be emptied or unloaded without damage that would prevent it from being used again.
Reuse is defined as any operation by which a reusable packaging is used multiple times for the same purpose for which it was originally designed.
Within the PPWR framework, reuse refers to repeated use of packaging for its intended purpose. Therefore, the packaging must be designed to enable reuse, incorporate recycled content, and be recyclable at the end of its life cycle.
Trade-offs may be required in terms of additional weight or volume, for example when more robust and thicker packaging is necessary to support multiple uses.
Refilling is defined as an operation in which a container used as packaging—either owned by the end user or purchased by the end user at the point of sale—is refilled by either the end user or the final distributor with one or more products purchased from that distributor.
Transport and Sales Packaging:
- By January 1, 2030, at least 40% of transport packaging must be recyclable. This includes pallets and their wrapping, crates, drums, and barrels.
- By January 1, 2040, at least 70% must be recyclable.
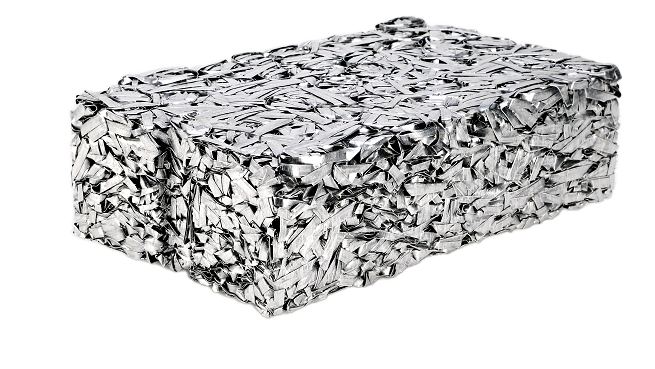
Grouped Packaging:
- By 2030, at least 10% of grouped packaging (excluding cardboard) must be reusable.
- By 2040, this target increases to 25%.
Beverage Packaging:
- By 2030, 10% of alcoholic and non-alcoholic beverages must be sold in reusable packaging.
- By 2040, the target rises to 40%.
- By 2034, the European Commission will assess the effectiveness of these targets to determine their feasibility.
Reuse, refill, and return systems allow consumers to reuse a container—whether personal or provided—at a point of sale or a dedicated station. These mechanisms are envisioned as effective alternatives to single-use, offering a substantial reduction in packaging waste. It is therefore essential to begin rethinking current models, especially in logistics, and to consider more circular approaches.
Packaging and substances of concern
Article 5 states that packaging placed on the market must be manufactured to minimize the presence and concentration of substances of concern in the materials used or their components. This includes emissions and by-products resulting from waste processing (e.g. secondary raw materials, ashes, and other materials destined for final disposal), as well as environmental impacts related to microplastics.
By December 31, 2026, the European Commission, assisted by the European Chemicals Agency (ECHA), will publish a report on the presence of substances of concern in packaging and its components, assessing their potential negative effects on reuse and recycling processes or chemical safety. The report may list these substances and evaluate whether they pose an unacceptable risk to human health or the environment.
In the EU, chemical substances—including those present in packaging—are already subject to upstream restrictions through key regulatory frameworks, such as:
- Regulation (EC) No 1907/2006 (REACH)
- Regulation (EC) No 1272/2008 (CLP)
- Regulation (EC) No 1935/2004, regarding packaging intended for food contact.
The EU Chemicals Strategy for Sustainability aims to build upon this regulatory foundation and develop coherent, complementary approaches to assess and manage chemical substances more effectively.
Packaging Labelling
According to Article 12, by August 12, 2028, all packaging placed on the market must bear harmonized labeling that provides information on the materials used, to facilitate sorting by consumers.
In addition to the required label, economic operators may include a QR code or other standardized digital data format on the packaging. This code can provide component-specific information to further guide consumers in separating and sorting packaging waste correctly.
Since 1997, packaging material identification has been governed by European Commission Decision 97/129/EC, which assigns a code composed of an abbreviation and number to each material or composite. A composite packaging refers to packaging made from different materials that cannot be separated manually, and in which no single material exceeds a specific weight threshold, as defined under Article 21 of Directive 94/62/EC.
With the new regulation, harmonized labels, QR codes, or any other type of standardized open digital data carrier must be affixed, printed, or engraved in a visible, legible, and durable manner on the packaging, in such a way that they cannot be easily removed or erased.
By August 12, 2026, the implementing acts are expected to be published, which will define the harmonized labeling requirements as well as the method for identifying the materials composing the packaging.
Starting August 12, 2028, packaging placed on the market must comply with harmonized labeling in accordance with the forthcoming implementing acts. In addition to material identification, harmonized labels are expected to include:
- Accessibility pictograms, corresponding to labels on waste bins;
- Digital marking of substances of concern;
- Clear and unambiguous labeling for compostable packaging;
- QR codes indicating compliance with Extended Producer Responsibility (EPR) requirements;
- Recycled content disclosure, in line with EU specifications;
- Disclosure of bio-based plastic content, following harmonized rules.
As of February 12, 2029, reusable packaging must be clearly labeled as such and easily distinguishable from single-use packaging, allowing consumers to identify it immediately.
Some packaging types are exempt from these rules, notably:
- Packaging used in e-commerce,
- Transport packaging,
- Deposit return systems (DRS),
- Medical packaging where safety issues arise.
Additional labeling rules may apply depending on the intended use of the packaging, the type of product, or substances contained. For example, Amendment (EU) 2024/2865 to Directive (EC) No 1272/2008 on classification, labeling, and packaging of substances and mixtures introduced minimum label and font size requirements based on packaging volume (as detailed in Annex I).
EU declaration of conformity
Article 39 establishes the requirement for an EU Declaration of Conformity, based on the template in the annex of the regulation. This document must be prepared by the manufacturer, and certifies compliance with the requirements of Articles 5 to 12, or those adopted under them.
Registration
By February 2026, the European Commission will define a standardized registration format, enabling vendor-independent data transfers using open standards and machine-readable data.
Representative and Oversight Authority
The PPWR requires that each EU Member State designate a competent authority by July 2025 to oversee the implementation of the registration process.
This applies to:
- Any producer placing packaging or packaged products on a Member State’s market for the first time;
- Any entity unwrapping or unpacking products.
Producers must register in the Member State where they place their packaging or packaged products on the market.
If a producer is not established within the EU, they must appoint an authorized representative (AR) in that Member State.
Packaging for the Transport of Dangerous Goods
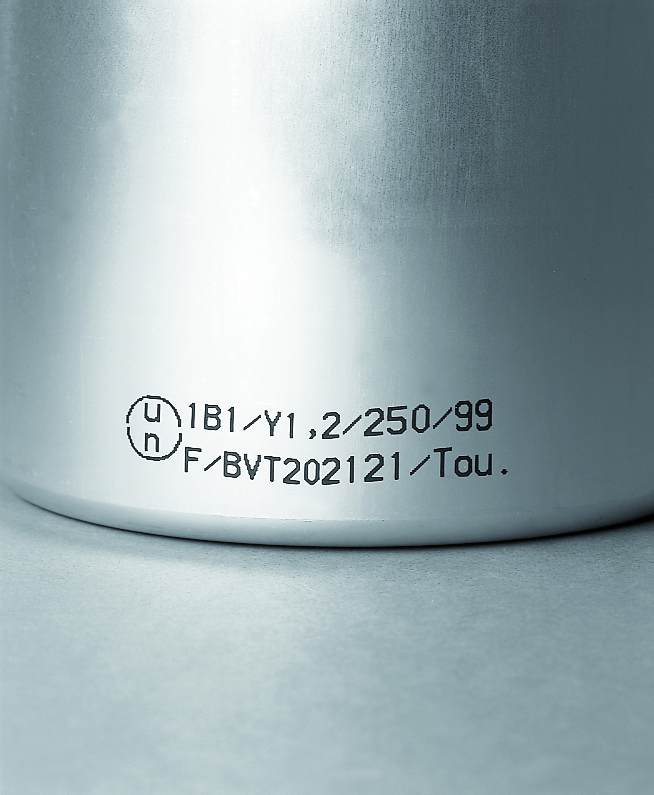
These types of packaging are often more complex in design to provide enhanced strength, durability, and functionality. They are subject to UN approvals and rigorous manufacturing inspections. In addition to containing and protecting transported products, these packages also serve as environmental safeguards, due to their high resistance to impacts, falls, pressure, etc., thus preventing spills and environmental contamination in the event of accidents.
The PPWR acknowledges this and states that in case of conflict with Directive 2008/68/EC on the transport of dangerous goods, the latter shall prevail.
The same applies to end-of-life management: if sufficient cleaning is not performed to remove residual hazardous substances, the packaging becomes hazardous waste. The PPWR applies without prejudice to Directive 2008/98/EC of November 19, 2008, on waste management.
In these cases, packaging performance takes precedence over recyclability, and TOURNAIRE recommends conducting a full environmental impact assessment of the product to evaluate whether it offers greater long-term sustainability.
Such an assessment provides a comprehensive view of environmental impacts, going beyond the carbon footprint alone.
Packaging for Human and Veterinary Medicines
According to Directive 2001/83/EC of the European Parliament and of the Council of 6 November 2001, establishing a Community code relating to medicinal products for human use, primary packaging is defined as:
“the container or any other form of packaging that is in direct contact with the medicinal product.”
A medicinal product is defined as any substance or combination of substances:
- Presented as having curative or preventive properties for human diseases;
- Or which may be administered to diagnose, restore, correct, or modify physiological functions in humans.
The REGULATION (EU) 2019/6 of 11 December 2018, on veterinary medicinal products, repealing Directive 2001/82/EC, defines primary packaging similarly as: “the container or any other form of packaging that is in direct contact with the veterinary medicinal product.”
For packaging intended for human and veterinary medicines, in order to protect human and animal health and ensure safety, due to the nature of the packaged products and the related requirements, PPWR obligations on recyclability and related aspects should not be mandatory. Compliance must instead be assessed with priority given to the two applicable legislative texts.
A Major Step Forward for the Environment
The PPWR represents a major environmental advancement. It aims to reduce single-use packaging, preserve natural resources, limit CO₂ emissions, and support a coherent and transparent circular economy.
For companies, this means a complete rethinking of packaging: lighter, more recyclable, better designed, and adapted for reuse or refilling. Standardized labeling becomes mandatory. The Extended Producer Responsibility (EPR) mechanism becomes a structural economic tool, incentivizing eco-design.
These obligations require significant logistical and industrial investment, but also stimulate innovation, skill development, and offer real opportunities for differentiation and improved environmental performance.
Global Developments
Asia-Pacific countries are also taking steps to reduce hazardous chemicals in products.
In Q1 2025, more than 30 Asia-Pacific nations — including India, Japan, Thailand, and Vietnam — signed the Jaipur Declaration of March 2025 on the 3Rs and Circular Economy, launching a 2025–2035 roadmap.
This non-binding declaration aims, among other goals, to reduce hazardous chemicals and persistent organic pollutants (POPs) in materials, products, and waste, including plastics. It follows the Hanoi 3R Declaration (2013–2023), which provided a general policy framework for the development and implementation of Reduce, Reuse, Recycle (3R) strategies across the Asia-Pacific region. The new declaration sets out 13 voluntary goals, one of which specifically addresses the elimination of hazardous substances.
Europe’s Forward-Looking Vision
With the PPWR, Europe demonstrates strong environmental ambition and commitment, introducing innovative standards and targets designed to revolutionize packaging production, usage, collection, and recycling.
Often a pioneer in structuring packaging regulations, the EU sets an example that will hopefully inspire broader global adoption of the 3R sustainability principles.
Thanks to its strong export focus and long-standing commitment to sustainability, TOURNAIRE and its aluminum packaging solutions position themselves as a preferred partner in this transition, offering solutions that comply with the new regulation.
Key Takeaways
-
- From January 1, 2035: Packaging must also be recyclable at scale. The methodology to assess large-scale recyclability by packaging category will be defined by an implementing act adopted by January 1, 2030.
- From January 1, 2038: Packaging with a C-grade performance will be banned from the EU market.
- From January 1, 2030: All packaging placed on the market must be recyclable.
- By January 1, 2028: The European Commission will issue secondary legislation defining Design for Recycling (DfR) criteria and recyclability performance levels based on predominant material.
- Packaging recyclability will be scored as:
- A (≥95%)
- B (≥80%)
- C (≥70%)
These scores will inform eco-modulation of EPR fees.
References
- DIRECTIVE 94/62/CE DU PARLEMENT EUROPEEN ET DU CONSEIL du 20 décembre 1994 relative aux emballages et aux déchets d’emballages
- RÈGLEMENT (UE) 2025/40 DU PARLEMENT EUROPÉEN ET DU CONSEIL du 19 décembre 2024 relatif aux emballages et aux déchets d’emballages, modifiant le règlement (UE) 2019/1020 et la directive (UE) 2019/904, et abrogeant la directive 94/62/CE
- DIRECTIVE 2008/68/CE DU PARLEMENT EUROPÉEN ET DU CONSEIL du 24 septembre 2008 relative au transport intérieur des marchandises dangereuses
- DIRECTIVE 2008/98/CE DU PARLEMENT EUROPÉEN ET DU CONSEIL du 19 novembre 2008 relative aux déchets et abrogeant certaines directives
- DECISION DE LA COMMISSION du 28 janvier 1997 établissant le système d’identification des matériaux d’emballage, conformément à la directive 94/62/CE du Parlement européen et du Conseil relative aux emballages et aux déchets d’emballages (Texte présentant de l’intérêt pour l’EEE) (97/ 129/CE)
- DIRECTIVE 2001/83/CE DU PARLEMENT EUROPÉEN ET DU CONSEIL du 6 novembre 2001 instituant un code communautaire relatif aux médicaments à usage humain (JO L 311 du 28.11.2001, p. 67).
- REGLEMENT (UE) 2019/6 DU PARLEMENT EUROPÉEN ET DU CONSEIL du 11 décembre 2018 relatif aux médicaments vétérinaires et abrogeant la directive 2001/82/CE (JO L 4 du 7.1.2019, p. 43).
- RÈGLEMENT (CE) N° 1907/2006 DU PARLEMENT EUROPÉEN ET DU CONSEIL du 18 décembre 2006 concernant l’enregistrement, l’évaluation et l’autorisation des substances chimiques, ainsi que les restrictions applicables à ces substances (REACH), instituant une agence européenne des produits chimiques, modifiant la directive 1999/45/CE et abrogeant le règlement (CEE) n° 793/93 du Conseil et le règlement (CE) n° 1488/94 de la Commission ainsi que la directive 76/769/CEE du Conseil et les directives 91/155/CEE, 93/67/CEE, 93/105/CE et 2000/21/CE de la Commission
- RÈGLEMENT (UE) 2024/2865 DU PARLEMENT EUROPÉEN ET DU CONSEIL du 23 octobre 2024 modifiant le règlement (CE) no 1272/2008 relatif à la classification, à l’étiquetage et à l’emballage des substances et des mélanges
- RÈGLEMENT (CE) No 1935/2004 DU PARLEMENT EUROPÉEN ET DU CONSEIL du 27 octobre 2004 concernant les matériaux et objets destinés à entrer en contact avec des denrées alimentaires et abrogeant les directives 80/590/CEE et 89/109/CEE
Want to Know More? Contact the Tournaire Experts
Our guide has given you an overview of the latest developments in PFAS regulations as well as Tournaire’s excellence in providing safe and innovative packaging solutions. If you would like to explore in more detail how our products and services can meet your specific needs, we are here to help.
Our experts are available for personalized consultations.
Visit our contact form to share your needs and questions with us. A member of our team will respond as quickly as possible to provide you with expert advice tailored to your industrial context. Tournaire is committed to providing not only high-quality products but also support and expertise that make a difference. Contact us today to move your project forward with a partner you can rely on.